การประกอบกิจกรรมการผลิตในสถานประกอบการมักมีการทำงานเกี่ยวข้องกับสารเคมีซึ่งอาจส่งผลกระทบเสียหายแก่สุขภาพของผู้ปฏิบัติงานได้ หากได้รับสารเคมีที่มีความเป็นอันตรายเข้าสู่ร่างการ การดำเนินงานเจ้าของกิจการหรือนายจ้าง รวมทั้งคนงานควรเอาใจใส่กับการป้องกันไม่ให้สารเคมีก่อผลเสียหายต่อสุขภาพ ซึ่งเป็นเรื่องที่กฎหมายได้กำหนดข้อปฏิบัติไว้แล้วด้วย
ข้อกำหนดตามกฎหมายความปลอดภัยในการทำงาน
ประกาศกระทรวงมหาดไทย เรื่องความปลอดภัยในการทำงานเกี่ยวกับภาวะแวดล้อม (สารเคมี) พ.ศ. 2520 กำหนดหน้าที่ของนายจ้างไว้ว่า ให้จัดการดูแลให้บรรยากาศในที่ทำงานมีปริมาณสารเคมีเจือปนได้ไม่เกินเกณฑ์ที่ประกาศไว้ เช่นห้ามมิให้นายจ้างให้ลูกจ้างทำงานในที่ที่มีปริมาณความเข้มข้นของสารเคมีในบรรยากาศเกินกว่าที่กำหนด และถ้ามีปริมาณความเข้มข้นของสารเคมีในบรรยากาศของการทำงานเกินกว่าที่กำหนดไว้กำหนด ให้นายจ้างดำเนินการลดความเข้มข้นของสารเคมี ถ้าแก้ไขไม่ได้ นายจ้างจะต้องจัดให้ลูกจ้างสวมใส่อุปกรณ์ป้องกันส่วนบุคคล
ประกาศกระทรวงมหาดไทย เรื่องความปลอดภัยในการทำงานเกี่ยวกับสารเคมี พ.ศ.2534 กำหนดหลักเกณฑ์การทำงานเกี่ยวกับสารเคมีอันตรายที่นายจ้างต้องปฏิบัติ เช่น
- การขนส่ง เก็บรักษา เคลื่อนย้าย และกำจัดหีบห่อ ภาชนะบรรจุ หรือวัสดุห่อหุ้มสารเคมีอันตราย ต้องปฏิบัติตามหลักเกณฑ์และวิธีการกำหนด
- จัดให้มีฉลากขนาดใหญ่พอสมควรปิดไว้ที่หีบห่อภาชนะบรรจุหรือวัสดุห่อหุ้มสารเคมีอันตรายทุกชิ้น ฉลากต้องมีรายละเอียดตามที่กำหนด
- จัดทำรายงานความปลอดภัย และการประเมินการก่ออันตรายของสารเคมีอย่างน้อยปีละหนึ่งครั้ง
- จัดสถานที่ทำงานของลูกจ้างซึ่งเกี่ยวข้องกับสารเคมีอันตรายให้มีสภาพและคุณลักษณะเหมาะสม เช่น มีการระบายอากาศที่ดี เป็นต้น
- จัดชุดทำงานสำหรับลูกจ้างที่ทำงานเกี่ยวกับสารเคมีอันตราย
- จัดให้มีที่ชำระล้างสารเคมีอันตราย เช่น ฝักบัว ที่ล้างตา ไว้ในบริเวณที่ลูกจ้างทำงานเกี่ยวกับสารเคมีอันตราย รวมทั้งอ่างล้างหน้า ล้างตา ห้องอาบน้ำ
- จัดให้มีการตรวจวัดปริมาณความเข้มข้นของสารเคมีอันตรายในบรรยากาศบริเวณสถานที่ทำงานและสถานที่เก็บเป็นประจำ
- จัดให้มีการอบรมลูกจ้างที่ทำงานเกี่ยวกับสารเคมีอันตราย
- จัดให้มีการตรวจสุขภาพลูกจ้างที่ทำงานเกี่ยวกับสารเคมีอันตราย
โอกาสที่คนงานจะได้รับสารเคมีอันตราย
คนงานที่ปฏิบัติงานในสถานประกอบการต่าง ๆ อาจเกี่ยวข้องหรือมีโอกาสสัมผัสสารเคมีได้หลายลักษณะ เช่น ภาชนะบรรจุแตกหรือมีรอยรั่ว หรือมีการหกกระจาย ระหว่างการขนย้าย การเก็บ การถ่ายเถใส่ภาชนะใหม่ หรือการกำจัดทิ้ง หรือจากการเกิดควันหรือก๊าซพิษ หรือการระเบิด ระหว่างการเก็บในพื้นที่จำกัด บางครั้งอาจปะปนมากับฝุ่นละออง รวมทั้งจากการซ่อมบำรุงรักษาอุปกรณ์เครื่องใช้ในการผลิตต่างๆ เป็นต้น
สารเคมีที่คนงานอาจสัมผัสอาจอยู่ในลักษณะของเหลว ของแข็ง ฝุ่น ไอระเหย ควัน หรือก๊าซ
การประเมินความเสี่ยงอันตรายจากสารเคมี
การประเมินว่าคนงานมีความเสี่ยงต่อการเจ็บป่วยหรือได้รับอันตรายจากสารเคมีอันตรายหรือไม่สามารถพิจารณาจากสิ่งต่อไปนี้
· พิจารณาว่าสารที่เกี่ยวข้องมีความเป็นอันตรายหรือไม่ อย่างไร จากข้อมูลเกี่ยวกับความเป็นอันตรายของสารเคมีที่ได้รับมา ได้แก่ จากเอกสารความปลอดภัยสารเคมี (MSDS) ฉลาก คู่มือ และเอกสารอื่น ๆ
· พิจารณาว่าในการใช้งานสารเคมีว่ามีการควบคุมไม่ให้เกิดอันตรายอย่างเพียงพอหรือไม่ จากผลการตรวจสอบกระบวนการผลิต เช่น มีการใช้สารเคมีตามข้อมูลที่ระบุมาในเอกสาร MSDS ที่ได้รับมาจากผู้ผลิตสารเคมี เป็นต้น
· พิจารณาว่าคนงานมีโอกาสจะได้รับสารเคมีในระหว่างการทำงานหรือไม่ มากน้อยเท่าใด จากการเฝ้าระวังปริมาณสารเคมีในบรรยากาศ ซึ่งเป็นระดับความเข้มข้นที่คนงานสัมผัสสารเคมี
· พิจารณาจากการติดตามเฝ้าระวังสุขภาพคนงานเพื่อให้ค้นพบผลกระทบของสารเคมีที่ทำให้สุขภาพเสื่อมเสียตั้งแต่ในระยะเริ่มต้น
หลักในการควบคุมและเฝ้าระวังอันตรายจากสารเคมีในการทำงานข้างต้นได้รับการบรรจุไว้ในประกาศกระทรวงมหาดไทย เรื่องความปลอดภัยในการทำงานเกี่ยวกับสารเคมี พ.ศ. 2534 แล้ว หากเจ้าของกิจการและคนงานปฏิบัติตามข้อกำหนดอย่างครบถ้วน
การลดความเสี่ยงอันตรายจากสารเคมี
วิธีการควบคุมโดยรวมเพื่อลดความเสี่ยงอันตรายจากสารเคมีที่ควรนำมาดำเนินการเรียงตามลำดับความสำคัญมีดังนี้
1. กำจัดหรือเคลื่อนย้ายสิ่งที่เป็นอันตรายออกจากที่ทำงาน ได้แก่ ไม่ใช้สารเคมีหรือสิ่งของที่ไม่จำเป็นต้องใช้ในโรงงาน
2. ใช้กระบวนการ อุปกรณ์หรือสารเคมีที่ปลอดภัยกว่าแทน
3. จัดให้มีพื้นที่สำหรับสารเคมีโดยเฉพาะแยกออกจากคนงาน โดยจัดพื้นที่เป็นระบบปิดสำหรับสารเคมี ย้ายคนงานหรือสิ่งกีดขวางต่าง ๆ ออก
4. ใช้การควบคุมทางวิศวกรรม เช่นการระบายก๊าซ เป็นต้น
5. ใช้มาตรการทางด้านบริหารจัดการ เช่น จำกัดเวลาทำงานของคนงานในบริเวณใกล้แหล่งที่มีอันตราย
6. ใช้อุปกรณ์ป้องกันส่วนบุคคล เช่นแว่นตากันสารเคมีและเครื่องช่วยหายใจ
การใช้อุปกรณ์ป้องกันส่วนบุคคลควรนำมาใช้ในกรณีที่ได้นำวิธีการที่ 1 – 5 มาใช้แล้ว แต่ยังคงมีความเสี่ยงต่ออันตรายสารเคมีอยู่ ไม่ใช่วิธีการที่นำมาใช้เป็นลำดับแรก
ตัวอย่างการควบคุมอันตรายจากสารเคมีในโรงงานชุบเคลือบผิว
การชุบเคลือบผิวชิ้นงานเป็นกระบวนการที่มีการใช้สารเคมีจำนวนมาก คนงานมีโอกาสสัมผัสหรือใกล้ชิดกับสารเคมีค่อนข้างสูงในการปฏิบัติงาน กระบวนการชุบและตัวอย่างสารเคมีที่เกี่ยวข้องมีดังนี้
สารเคมีและอันตรายที่อาจเกิดขึ้นได้
ในกระบวนการชุบเคลือบผิวซึ่งประกอบด้วยขั้นตอนพื้นฐานคือ (1) การเตรียมวัสดุเช่น การขัดแต่งให้เรียบ (2) กระบวนการก่อนชุบได้แก่ การยึดวัสดุที่จะชุบและจุ่มลงในบ่อก่อนชุบ ซึ่งมีสารละลายเคมีต่าง ๆ เช่น ด่างและกรด แล้วจุ่มล้างในบ่อน้ำล้าง (3) กระบวนการชุบคือ ขั้นตอนการจุ่มวัสดุลงในบ่อชุบและบ่อน้ำล้างตามลำดับ (4) กระบวนการหลังชุบ เช่นอาจเป็นกระบวนการเคลือบโครเมตเพื่อป้องกันสนิมได้แก่ ขั้นตอนการจุ่มวัสดุลงในบ่อหลังชุบและบ่อน้ำล้าง (รูปที่ 1)
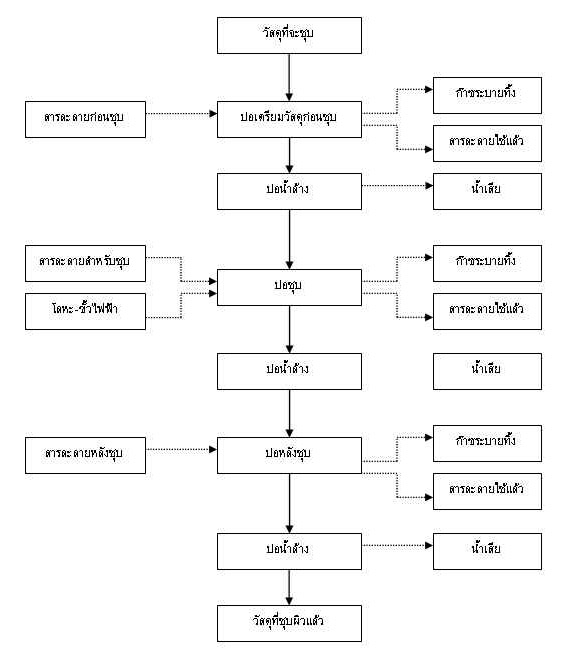 รูปที่ 1 ผังกระบวนการชุบเคลือบผิวด้วยไฟฟ้า (ดัดแปลงจาก http://www.prtr.nite.go.jp/english/pdf/manual2005/calc06-2e.pdf)
สารเคมีอันตรายที่ใช้และเกิดขึ้นในกระบวนการชุบโลหะด้วยไฟฟ้าประกอบด้วย
· สารทำละลาย เช่น เมทิลีนคลอไรด์ ฟีนอล กรดคริซิริก
· ก๊าซ เช่น ไฮโดรเจนไซยาไนด์
· กรด เช่น กรดโครมิก กรดซัลฟุริก และกรดไฮโดรคลอริก
· ด่าง เช่น โซเดียมไฮดรอกไซด์
· ไซยาไนด์ เช่น โซเดียมไซยาไนด์ และโปตัสเซียมไซยาไนด์
· โลหะหนัก เช่น นิกเกิล โครเมียม แคดเมียม และตะกั่ว
· ของเสียอันตราย
คนงานที่สัมผัสสารเคมีเหล่านี้อาจเกิดผลกระทบต่อสุขภาพได้ เช่น ในระยะสั้นอาจเกิดอาการระคายและแสบ คอ ปอด จมูก ดวงตาและผิวหนัง ส่วนในระยะยาวอาจเกิดผลกระทบต่อสุขภาพเช่น โรคหืด หัวใจ ปอด และประสาท ทำงานผิดปกติ และในบางกรณีอาจเกิดมะเร็ง นอกจากผลต่อสุขภาพคนงานที่เกิดจาการได้รับสารเข้าสู่ร่างการแล้ว ก๊าซที่ระบายออกจากกระบวนการเช่น ก๊าซไฮโดรเจน ถ้าไม่จัดเก็บหรือระบายก๊าซให้ดีก็อาจเกิดการระเบิดได้ หรือพาสารเคมีอื่นปนออกมากลายเป็นหมอกพิษได้
โอกาสที่คนงานอาจได้รับอันตรายจากสารเคมี
คนงานในโรงชุบอาจสัมผัสสารเคมีได้จากเหตุการณ์หรือการกระทำดังต่อไปนี้
· สารละลายในอ่างชุบกระเด็นใส่ในระหว่างเคลื่อนย้ายชิ้นงานลงหรือขึ้นจากอ่างชุบ
· ไอหรือควันก๊าซที่ฟุ้งกระจายรุนแรงซึ่งเกิดในกรณีของกรด ด่าง หรือสารเคมีชนิดอื่น
· ฝุ่นละอองที่หายใจเข้าไประหว่างการขัดและตัดแต่งชิ้นงาน
· เมื่อการระบายอากาศบริเวณบ่อชุบไม่เพียงพอ
· จากของเหลวหรือกากตะกอนที่ต้องเอาออกจากอ่างชุบ
· จากการบำรุงรักษาและซ่อมแซมอ่างชุบ
· จากของเสียเคมีที่จัดการไม่ถูกวิธี
การลดความเสี่ยงอันตรายจากสารเคมี
นอกจากวิธีการลดความเสี่ยงที่เป็นมาตรฐานดังกล่าวข้างต้นแล้ว การควบคุมจัดการเฉพาะที่สำหรับโรงงานชุบเคลือบผิวมีรายละเอียดเพิ่มเช่น การควบคุมอันตรายที่บ่อชุบ บ่อล้าง สามารถกระทำได้โดยใช้สารที่มีความเป็นอันตรายน้อยกว่าแทน ใช้ปั๊มถ่ายสารละลายลงในบ่อชุบแทนการเทจากภาชนะ และต้องล้างปั๊มให้สะอาดก่อนใช้ปั๊มสารเคมีชนิดอื่น ติดตั้งเครื่องระบายอากาศบริเวณบ่อที่ปฏิบัติงานเพื่อระบายหมอกและไอสาร ใช้สารลดการเกิดก๊าซระหว่างการชุบ ดูแลไม่ให้มีสิ่งของตกหล่นลงในบ่อปฏิบัติงาน ซึ่งจะทำให้สารกระเด็นมาโดนผู้ปฏิบัติงานได้ ตรวจสอบให้แน่ใจว่าเครน ตะขอเกี่ยว และลวดสลิงอยู่ในสภาพใช้งานได้ดี
นอกจากนี้มีข้อควรระวังในกรณีกรดและไซยาไนด์ หากสาร 2 ชนิดผสมกันจะเกิดระเบิดขึ้นได้ ดังนั้นต้องทำฉลากปิดภาชนะให้ชัดเจน จัดเก็บแยกห่างจากกันในที่ที่แห้ง และในกระบวนการชุบวัสดุที่จุ่มลงในบ่อกรดต้องล้างน้ำให้สะอาด ก่อนจุ่มลงในบ่อชุบซึ่งมีไซยาไนด์อยู่ รวมไปถึงการระบายสารละลายกรดและสารละลายไซยาไนด์ออกจากบ่อต้องมีระบบแยกจากกัน
ส่วนของเสียที่ออกจากสายการผลิตซึ่งส่วนใหญ่เป็นของเสียเคมี เช่น เกลือของโลหะต่างๆ กรด ด่าง และไซยาไนด์ หากไม่กำจัดให้ถูกต้องปลอดภัยก็อาจส่งผลกระทบต่อสุขภาพของบุคลากรในสถานประกอบการหรือต่อบุคคลอื่น ๆ ได้ ของเสียประเภทกรดและด่างต้องทำให้เป็นกลางก่อนกำจัด และของเสียที่มีโลหะปนเปื้อนอยู่ต้องตกตะกอนโลหะออกก่อนส่งไปบำบัดกำจัดต่อไป
เอกสารอ้างอิง :
www.safetyline.wa.gov.au/newsite/worksafe/media/pdf/guidnotes/Guide_electroplating.pdf
www.prtr.nite.go.jp/english/pdf/manual2005/calc06-2e.pdf
ประกาศกระทรวงมหาดไทย เรื่อง ความปลอดภัยในการทำงานเกี่ยวกับภาวะแวดล้อม (สารเคมี) พ.ศ. 2520
ประกาศกระทรวงมหาดไทย เรื่องความปลอดภัยในการทำงานเกี่ยวกับสารเคมี พ.ศ. 2534
ภาพประกอบ : Mr. Dave Pedigo and Mr. Ed Embry ,Ambrake Corporation ,Metal Finishing Industry Case Study
http://www.kppc.org/resources/workshops/MetalFinishing/presentations/Ambrake%20presentation.ppt#256,1,AMBRAKE CORPORATION
http://www.plating.co.nz/process.asp |